Aucun produit dans le chariot
9 SAFETY FOCUS AREAS TO REDUCE RISK OF SLIPS, TRIPS AND FALLS
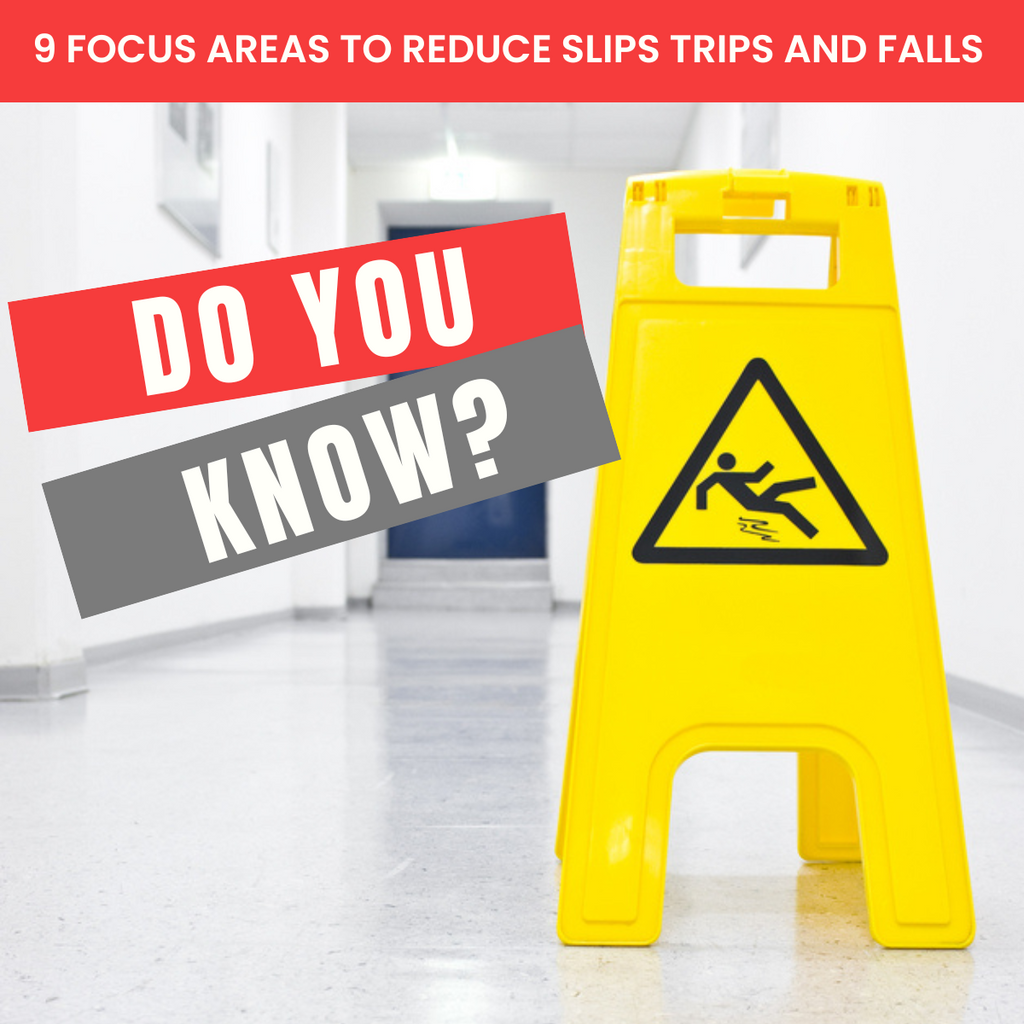
ADDRESS THESE FOCUS AREAS TO REDUCE THE RISK OF WORKPLACE SLIPS, TRIPS AND FALLS.
- Seasonal hazards. Identify areas on your worksite where snow, ice and other slippery conditions may occur. Clear and maintain these areas.
- The impact of “transitions”. When it comes to STF hazards, it’s also important to be mindful of transition zones. There has been a strong correlation made between slips and falls and a range of “transitions”. “From winter to spring, from spring to winter, from a warm factory to freezer, from inside to outside; this is where and when they are more likely to happen. Identify key transitions and develop a plan specifically to manage them.
- Spills. Make sure there’s a practice in place for every spill to be cleaned up as quickly as possible and according to safe work practices for the material spilled.
- Flooring Request that workers report any damaged flooring to supervisors. Employers should have someone attend to the damage and ensure the area is marked and barricaded until repair or maintenance is complete.
- Ongoing housekeeping. Continuous housekeeping is essential to avoiding many workplace hazards. Keeping work areas in order, removing waste materials and other fire hazards, are just a few ways housekeeping can be maintained.
- Company policy. Every workplace should have a policy in place that details the rules for housekeeping and inspections and ensures the requisite personal protective equipment (PPE), and other equipment, is worn and used properly. For Dale Harris, implementing policy changes have been an important part of his company’s proactive journey toward safety. One of their policies involves preventing anyone from walking on untended walkways and having people in place whose job is to make sure walkways are cleared in winter.
- Training & Supervision. A workplace that is prone to STFs should provide workers with proper training on how to clean up spills, use PPEs and work-related tools, machinery and any other equipment. According to the AB Canada Report, it’s important to make sure workers are completely trained to perform their work safely and that they know emergency response procedures inside, out and backwards. Ensure that supervisors work with individuals under their control and that feedback is given to workers after inspections and job observations. Supervisors should provide continuous follow-up to make sure that the training is sufficient and followed by staff, and to identify areas in need of improvement. Moreover, every accident should be investigated to avoid a recurrence.
- Organizational responsibility. Understanding and commitment of all levels of the company (employers, supervisors, workers, contractors, etc.), can be a challenge but is extremely important to successfully address safety issues.
- Wearing the correct PPE. PPE is worn by a worker to minimize exposure to specific hazards. Examples include respirators, gloves, aprons, fall protection, and full body suits, as well as head, eye and foot protection. Though only one element of a complete hazard control program, appropriate PPE are vital to employee safety protocols. Still, a corporate policy needs to do more than simply demand that PPE be worn. “Does the worker know what kind of footwear is required and why?”. “Does the supervisor know the requirements and actively enforce them?” "Does the employer ensure that the required footwear is included in their program and ensure the supervisor is confident that the program is being followed”." Answers to all those questions are imperative to a safe workplace environment. Always be mindful of the kind of PPE or footwear that is most appropriate given the hazards of the workplace. Companies may give directions on what kind of footwear is required and a reimbursement amount per year, which can be helpful. Comfort is essential too. “
Get our complete white paper: Creating a Complete Slip, Trip and Fall Plan for Your Workplace, by contacting us at biz@mistersafetyshoes.com